こんにちは、MIBです!
以前アイロンを使ったヒートプレスを紹介しました。
電気コンロなど大がかりな機器を使わずに、比較的家庭にあるであろうアイロンを使ってプラ板を軟化させることでお手軽にヒートプレスするというものでした(詳細はこちらの記事をご参照ください)。
ただ前回紹介した方法だとスポンジで加圧して形状に沿わせるので、作業中焦ってしまうしどこまで押し込めばよいかわかりにくく、結構難易度が高く感じました。
今回はその解決方法を紹介します。
解決方法
結論から言うと、プラ板で枠を作り、枠を押し付けることでヒートプレスする、という内容になります。
この方法、結局は通常のヒートプレスの方法そのままなので、文章にしてしまうと「なんで最初からやらなかったの」と感じるかもしれません。
ですが通常のヒートプレスとはプラ板を温める手法の違いから前回作業時は枠を使うことはできないと考えてしまっていました。
次から詳細を説明します。
通常のヒートプレスとアイロンヒートプレスの違い
通常のヒートプレスは、電気コンロなど熱を発するものにプラ板を近づけることでプラ板を軟化させます。
その際プラ板を単体で温めてしまうと手にまで熱が伝わり、熱くて作業どころではなくなってしまいます。
そのため通常のヒートプレスでは何かしらプラ板を保持して加熱する必要があり、枠を使うことはほぼ必須となります。
一方でアイロンヒートプレスは、熱を発するアイロン自体をプラ板に近づける(押し付ける)ことでプラ板を軟化させます。
そのためプラ板は単体で温める必要があり、加熱時に枠を使うことができません。
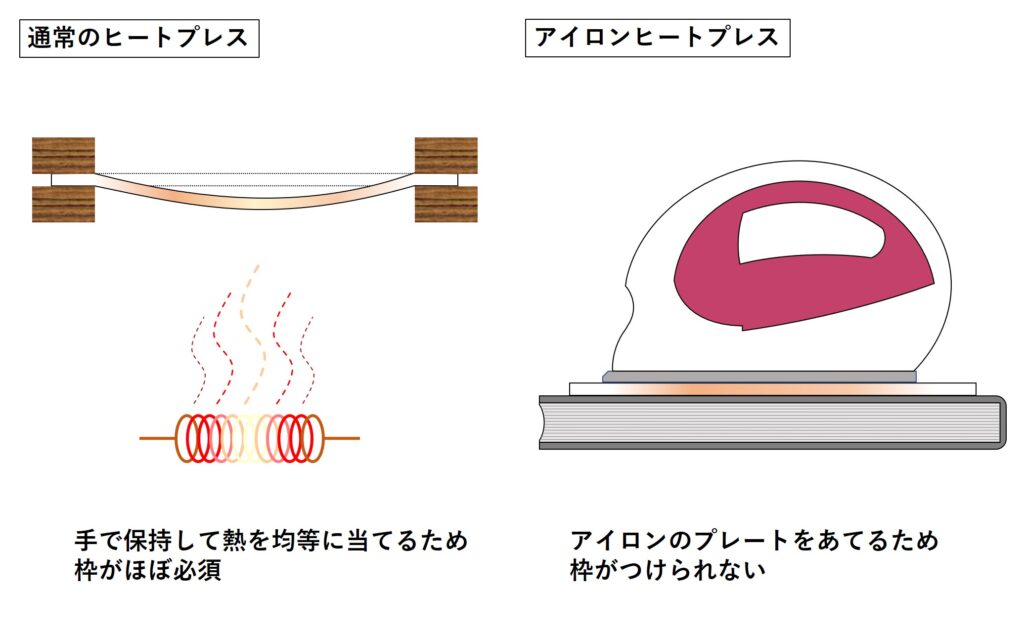
枠の付け方
上記の理由から枠を付けられずに軟化させたプラ板を原型になじませるためにスポンジで押し付けるようにしたのが前回の紹介内容でした。
ただし冒頭に述べたように作業中焦ってしまうし、どこまで押し込めばよいかわかりにくいという欠点があったため、通常のヒートプレスを参考に枠を付けられないか考えてみました。
いろいろ考えた結果、枠に両面テープを貼り付けておき、アイロンで軟化させたプラ板を、枠に貼り付けた両面テープでピックアップする、という非常に単純な方法でうまくいきました。
また、通常のヒートプレスとは異なりアイロンヒートプレスはプラ板単体で加熱、軟化させることができるので以下のメリットがありました。
- 枠自体は加熱されることがないので、使い慣れたプラ板で枠を作ることができる
- プラ板単体で均等に加熱できるため、枠は同一平面でなく、短冊形状の板を両面テープでロの字に貼り合わせたもので十分機能する
これらは枠製作のハードルを下げて、材料使用量も適正化できるので非常に大きなメリットだと感じています
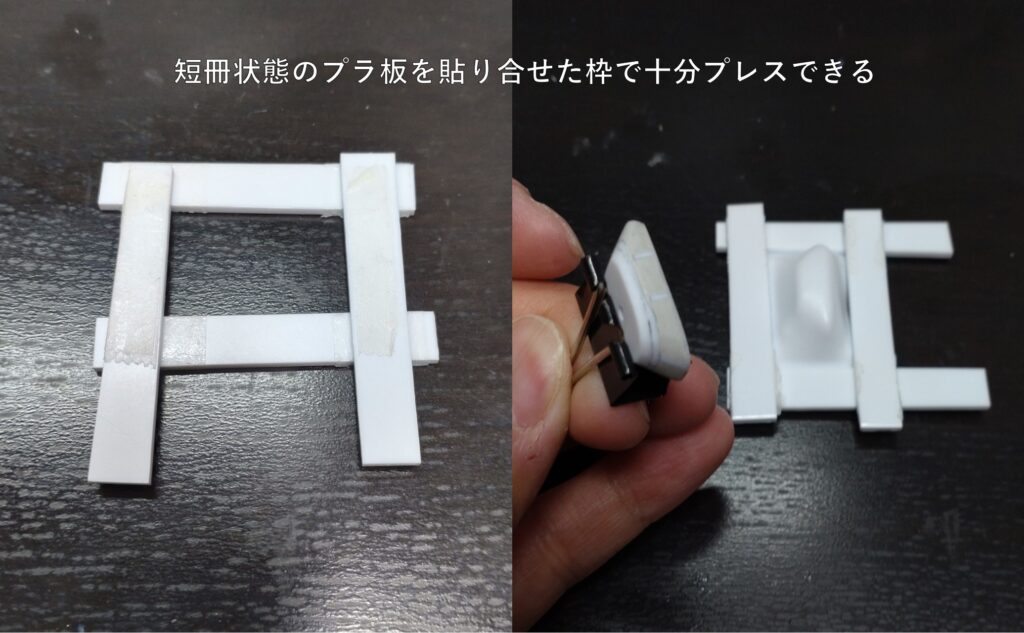
デスフィズ背面部の製作
実例として最初に取り組んだデスフィズ背面部を紹介します。
ここではこの記事で作成した原型を使ってアイロンヒートプレスしていきました。
背面部は深い絞り形状になっているので1回のヒートプレスで1部品を成形するのは困難だと考えて、背面と側面4方向に分けて作成することにしました。
背面は原型に直接プラ板を貼り付けて側面を面一になるように原型に合わせて削り込んでおきました。
その状態で側面4方向を枠を使ったアイロンヒートプレスで成形しました。
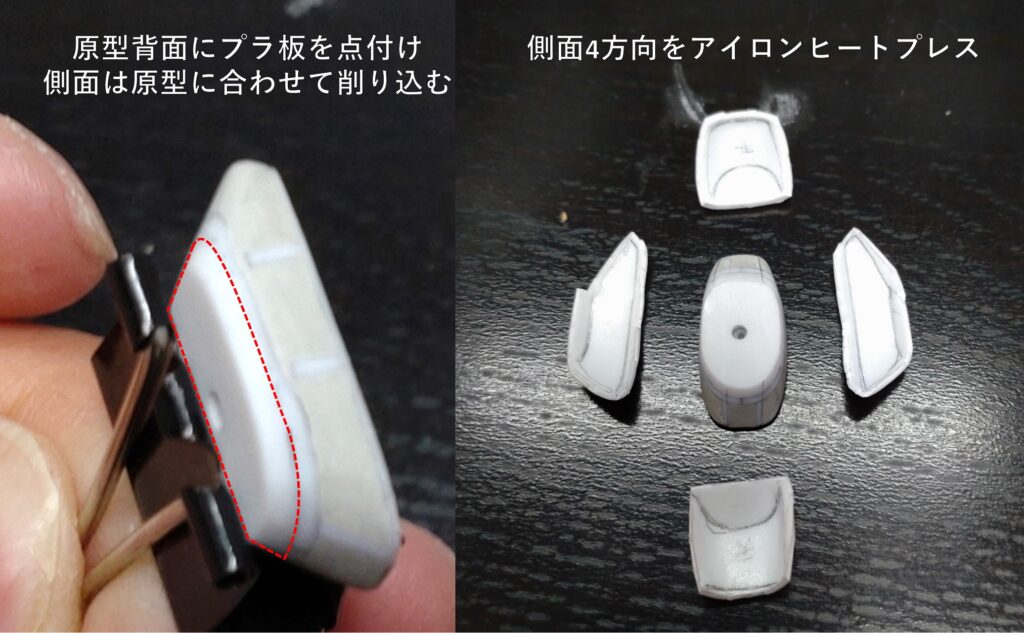
側面4方向の板を背面のプラ板に接着し、硬化後原型から外して隙間を瞬着で埋めました。
4方向からのプレスを行うとどうしても合わせ目をきっちり合わせることができないため、多少隙間が空くようにして埋めています。
また裏面には瞬着が回ってほしくないため、マスキングテープで保護しています。
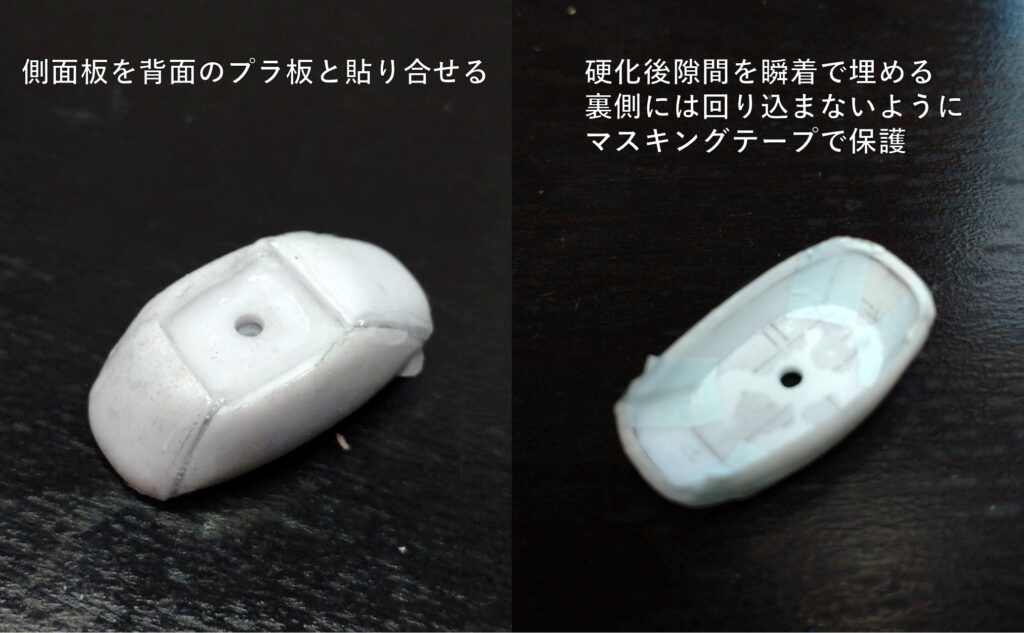
背面にはヒートプレスした際の形状が残っているので、隙間埋めの瞬着が硬化したら背面を部品形状になるように削り出します。
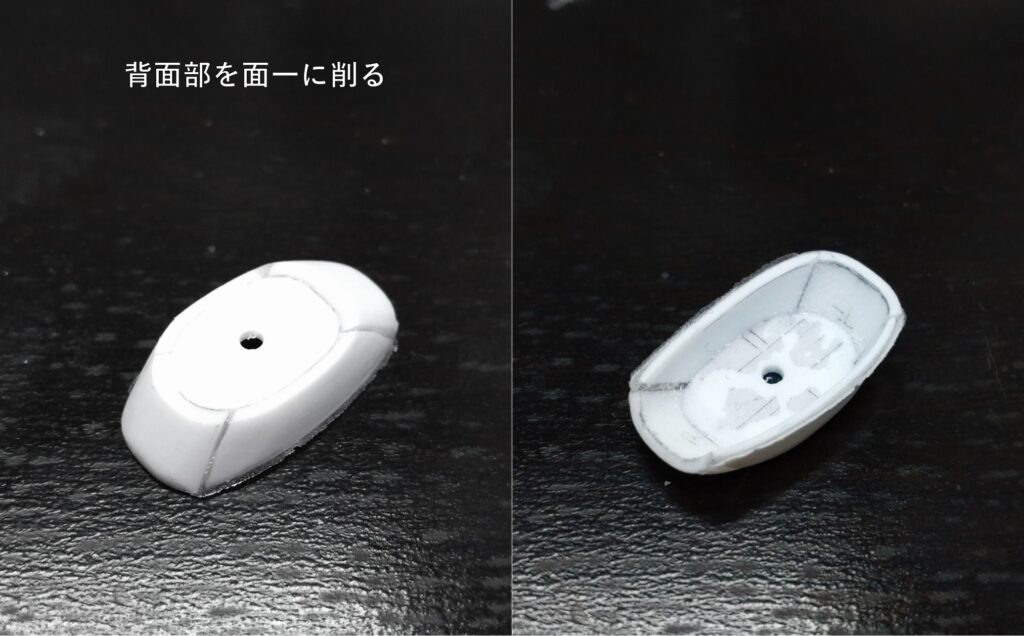
さらに背面にはGNドライブのような推進器がつくので、その形状を避けるような穴を開けたプラ板を貼り付けて、部品形状を整えます。
背面と側面の板の接着、側面同士の隙間埋めの効果待ち時間はありましたが、作業としてはそれほど困ることなく進みました。
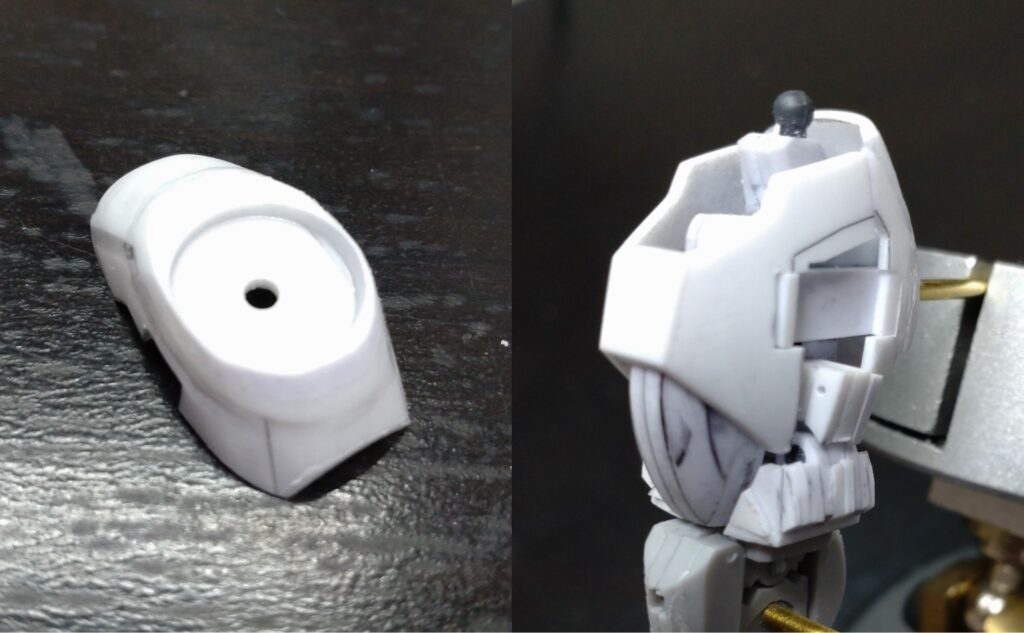
■さいごに
手軽にできる熱加工であるアイロンヒートプレスの作業性が改善されて、より手軽にできるようになったと思います。
プラ板の熱加工は慣れるまでは敷居が高い気がしますが、やってみると削り出しでは表現できない形状が手軽に作れて非常に効果が高いと感じています。
みなさんもぜひトライしてみてください。
ではっ!
コメント