こんにちは、MIBです。
初めて型取り・複製を行う場合の難所はいくつかあり、前回は費用についてまとめました。
今回は部品の配置について私の考えを書いてみたいと思います。
部品配置を習得する一番の方法
最近は型取り・複製を指南する解説本やブログも多く、非常に参考になる技術をたくさん目にすることができます。
ただその結果、高い確率で「難しくてまだ手を出すのは早い」「完全に理解できていないのでもっと勉強しないと」と感じてしまい、やってみることができなくなることもあります。私もそうでした。
私自身型取り・複製を頻繁にやる方ではないですが、やっている中でわかったことがあります。
それは
- 部品配置の考え方の習得は、やりながら自分で考えることが一番の近道
- うまく配置できず成形不良になりがちな部品は、別の型に新たに埋め込めばよい
という内容です。要は失敗を恐れずやってみればよい、という内容です。
ランナー状態で発売するガレージキットを作るならまだしも、自分のために型取り・複製をする場合、うまくいかなくても何回か流せばいいし、いくつか型を作ると思うのでうまく流れない部品は再度型取りする、最悪シリコンは余るはずなのでもう一度型を作る、という対処で、当初の目的である複製自体は問題なく行えると思います。
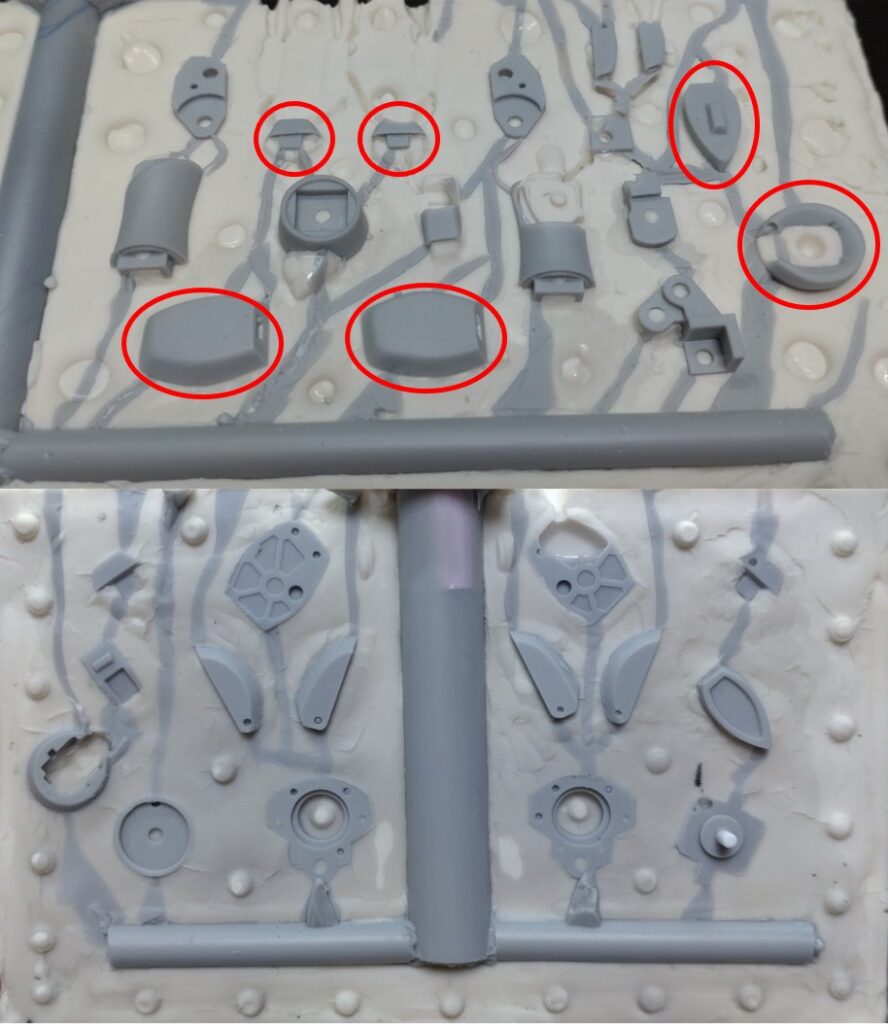
とはいえそれだけでは記事にまとめるには情報がなさすぎなので、次から私が実際にやっていて実感した内容についてまとめていきたいと思います。
配置で解消できる成形不良
複製時の成形不良は見た目上パーツ上にレジンが流れていない状況なのですが、その原因は次の4つに分類できると考えています。
- XY方向の気泡
- Z方向の気泡
- 空気が逃げられずに流れない
- 圧力が足りずに流れない
以下ではそれぞれの現象と対処法についてみていきます。
気泡
XY方向の気泡
型を開いた平面を私はXY平面と考えています。
XY方向気泡とは、この型を割った平面上に気泡が発生する現象です。
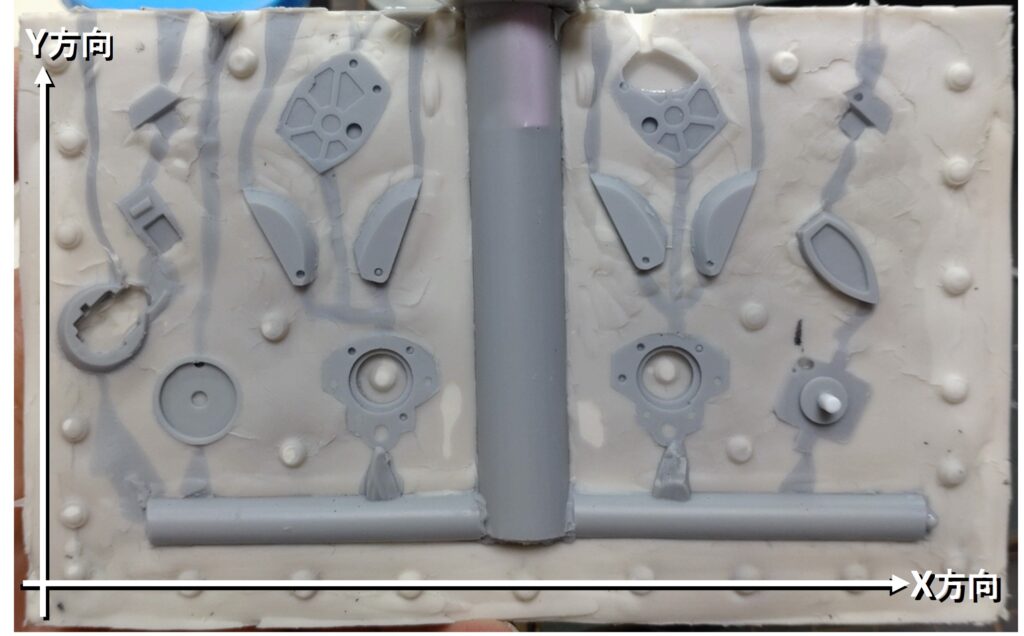
対処法
この対処は簡単で、レジンの流れに対して部品を傾けて配置し、一番頂点になるところに空気逃げを設ければほとんど発生しません。部品配置上の制約もあまりないので部品は積極的に斜めに配置するとよいです。
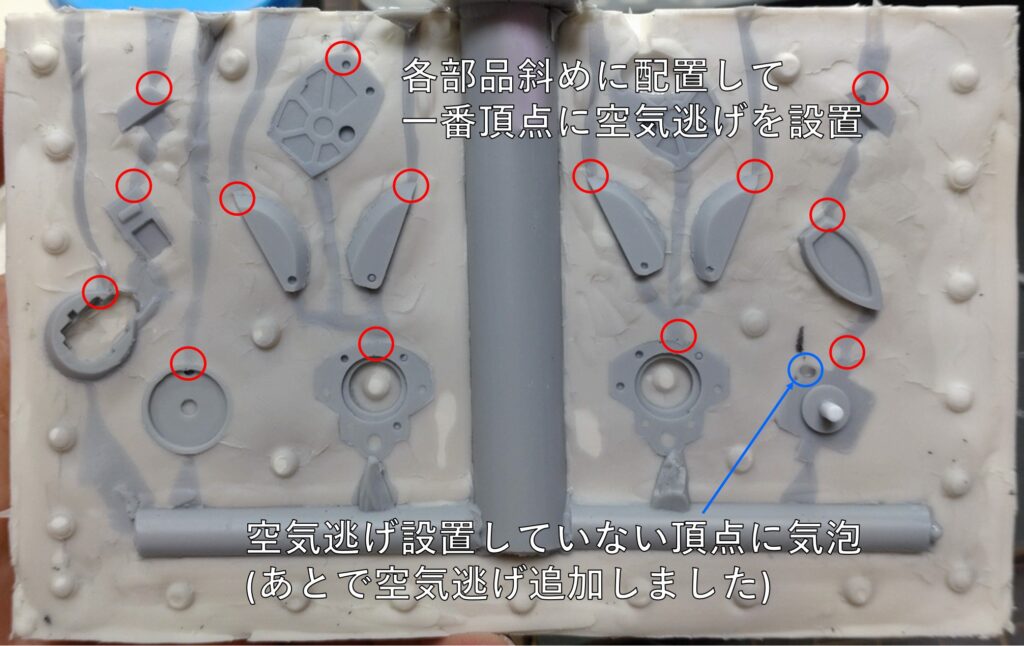
Z方向の気泡
型を割った平面をXYととらえているので、型の奥行方向はZ方向と考えています。
Z方向の気泡とは、この型の奥行方向で気泡が発生する現象です。
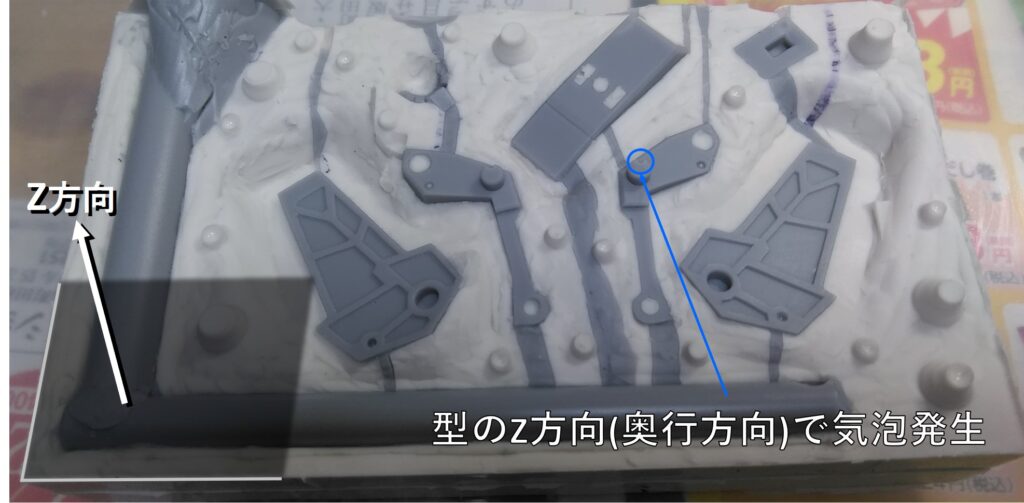
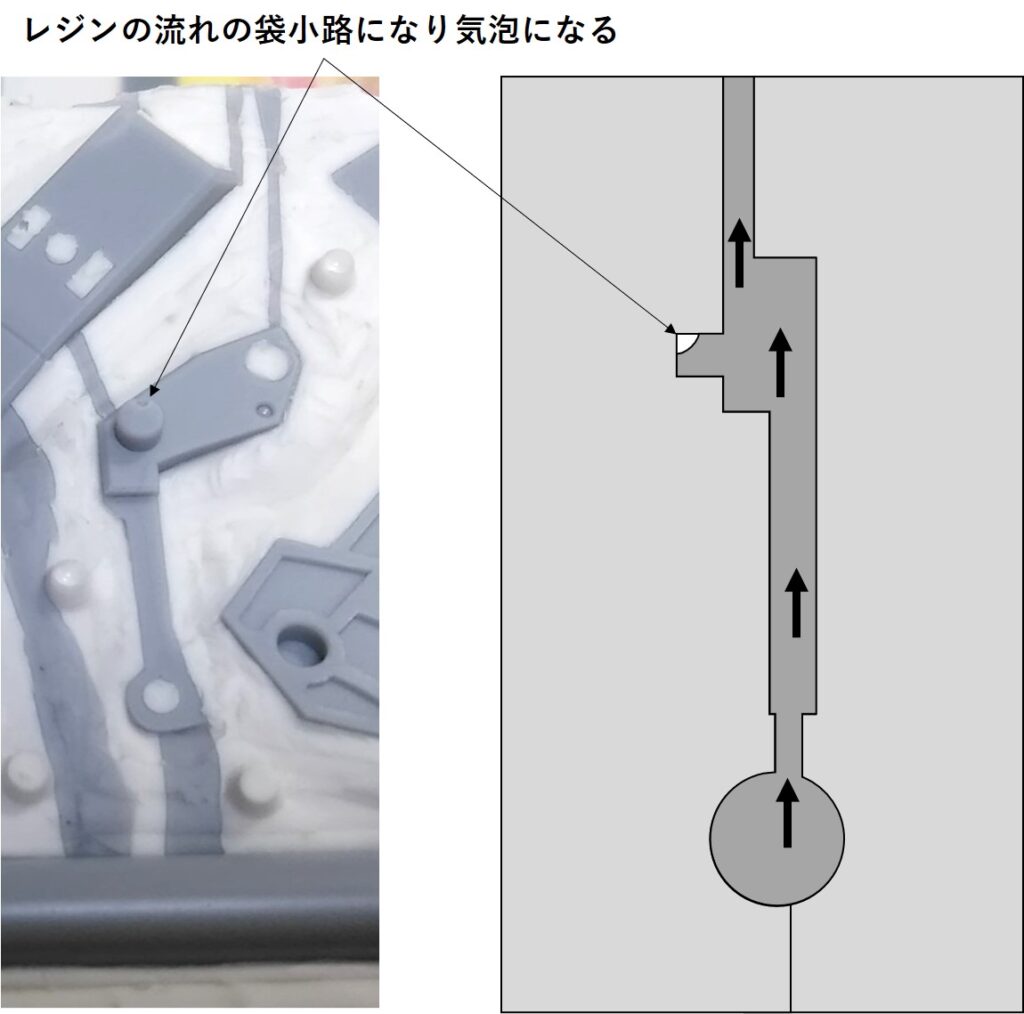
対処法
Z方向の気泡は、表面張力で流れていくことを期待してパウダーをまぶしておくことで対処するのが簡単です。
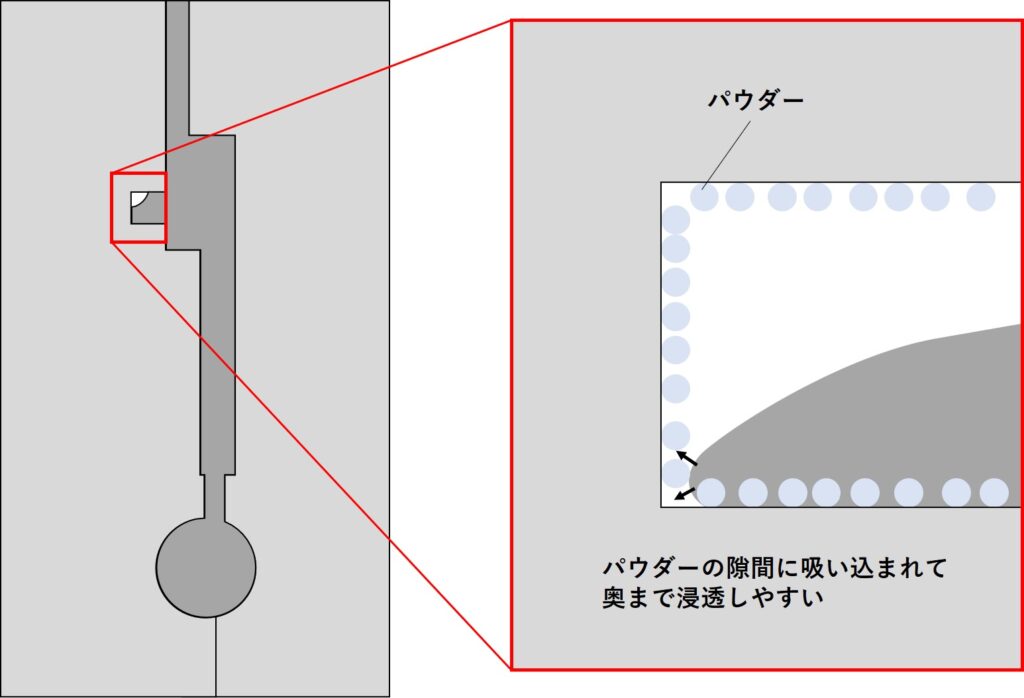
パウダーは私は瞬間接着パテ付属の粉を愛用しています。
Z方向の気泡も部品を傾ければ対処できこともありますが、XY方向と異なり型に埋め込む方向で部品を傾けることになるのでアンダーカットになる部分が増えることと、単純に粘土埋めが困難になるのでいつでも使える方法ではないです。
空気が逃げられずに流れない
単純に空気抜けがなければ流れませんが、空気抜けを作っていてもうまく空気が逃げられない場合があります。
部品内のレジン出口がふさがる
ゲートが複雑に入り組んでいると、レジンの流れ方によって部品内のレジン出口がふさがってしまうことがあります。
そうなるとその部品内の空気が抜けられずに、それ以上レジンが流れなくなってしまいます。
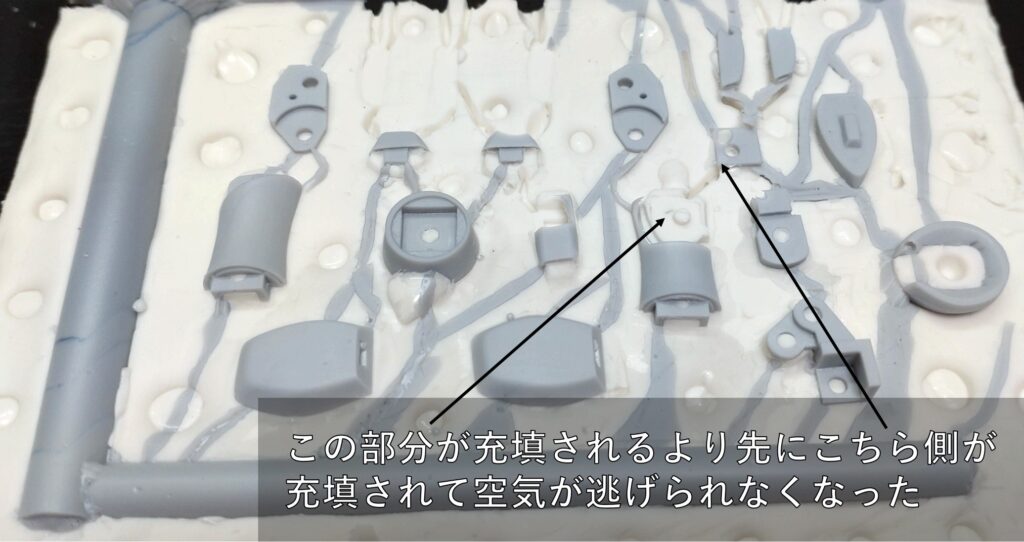
対処法
湯口から生やしたゲートは一方通行で出口に出るようにする
またレジン注ぎ口からあふれたレジンが空気抜き出口をふさいでしまうことがあります。こうなるとふさがれた部分から空気が抜けなくなるのでそのルートの部品にはレジンが流れなくなります。
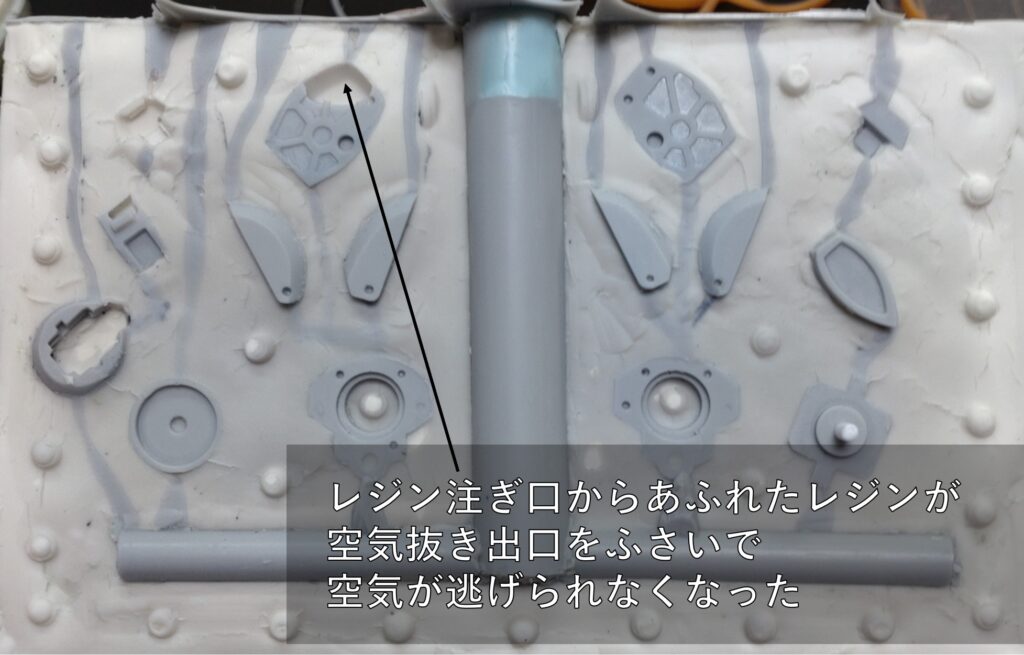
対処法
空気抜き出口にはレジンだまりを作っておく
圧力が足りずに流れない
これは本当にやってみて実感したのですが、レジンは流れる途中で圧力を損失するので、ただ流しただけでは湯口と同じ高さまで流しきることは難しいです。
身近な例でいうと、やかんに水を注ぐと、注ぎ口の水面は注いだ水と同じ高さになります。
しかしレジンは粘性が高いので、部品に回るレジンは注いだレジンと同じ高さにならず、ちょっと低い位置までしか進めません。
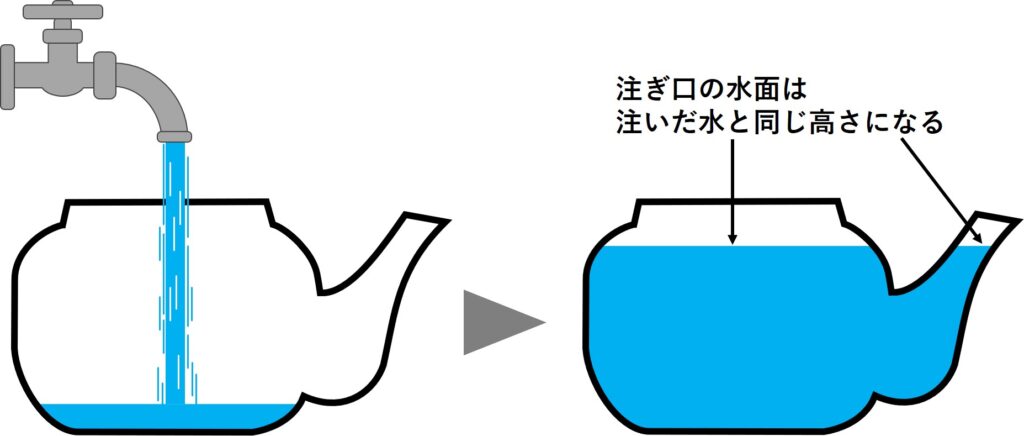
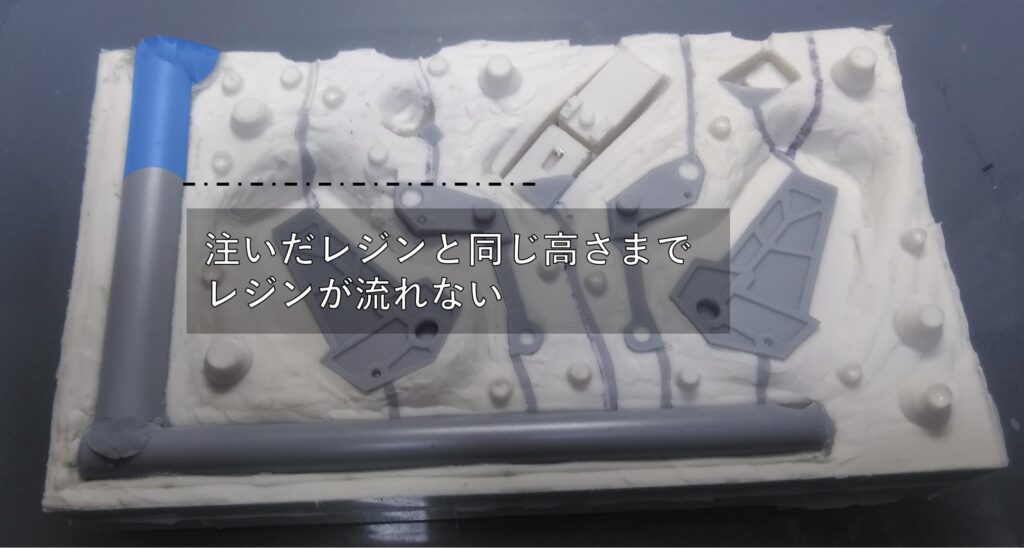
そのため特に湯口から離れた箇所に体積のある部品を配置すると、十分レジンが行きわたらないまま固まってしまいます。
特に湯口から離れた箇所にある、空気抜き出口に近い部分に体積のある部品を配置すると、その分に十分レジンが行きわたらないまま固まってしまいます。
対処法
- 湯口は型の中央に配置して遠くの部品への圧力損失を減らす
- 湯口から遠く、高い位置には体積のある部品は配置しない
またもしこの圧力損失が原因でレジンが流れない型を作ってしまった場合も対処法があります。
対処法
- 湯口の高さを稼いで、注ぐレジンを増やすことで圧力を補強する
- 湯口に前回の湯口を差し込み、注射器のように直接圧力をかけることでレジンを押し込む
1.の湯口の高さを稼ぐためには、100均に売っているタピオカストローが非常に良いです。
高さも任意で変えられるし、レジンが接着されないので何度も使いまわしもできるのでお勧めです。
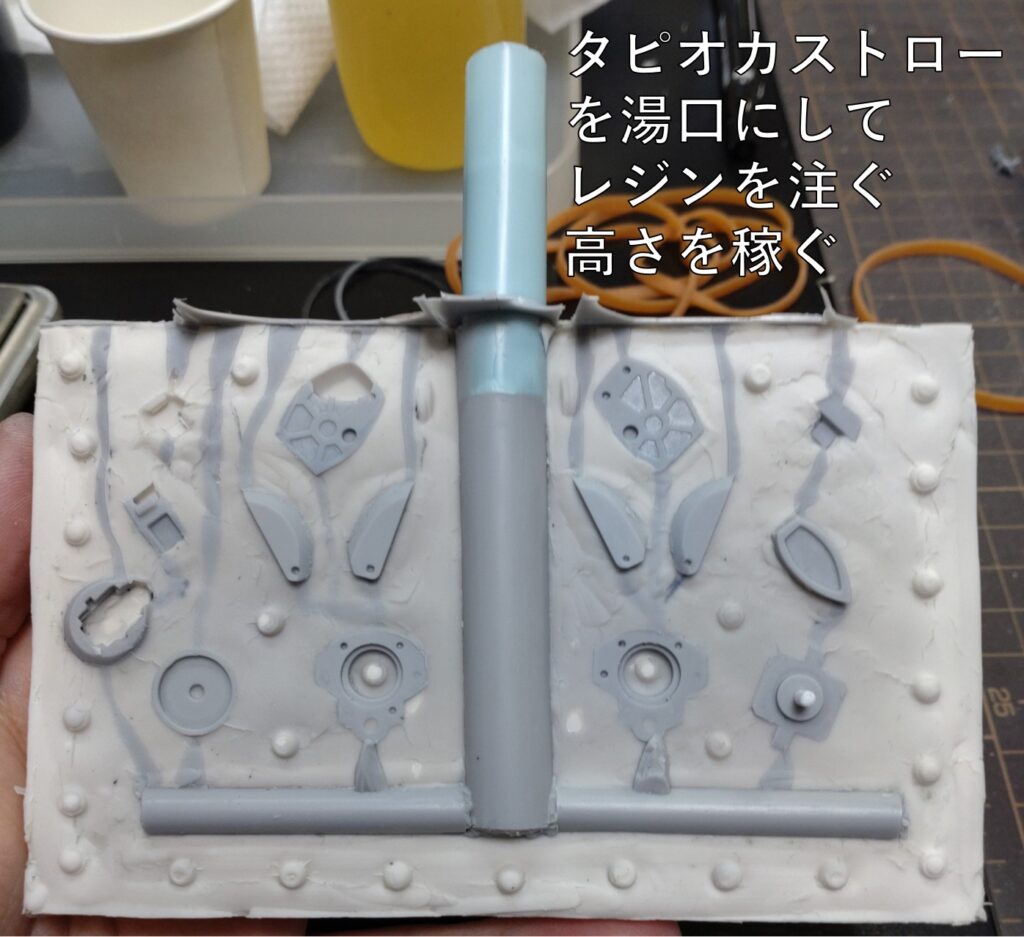
2.の前回の湯口を差し込む方法は多少強引ですが、しっかり押し込んでいる感じがして部品を作っている感が出ます。
また押し込む湯口ありきの方法なので初回はどうするんだという疑問もあるかと思いますが、初回はこの方法は使わずに単にレジンを流すだけにして、型のレジン流れの様子を観察するようにするので特に問題はないです。
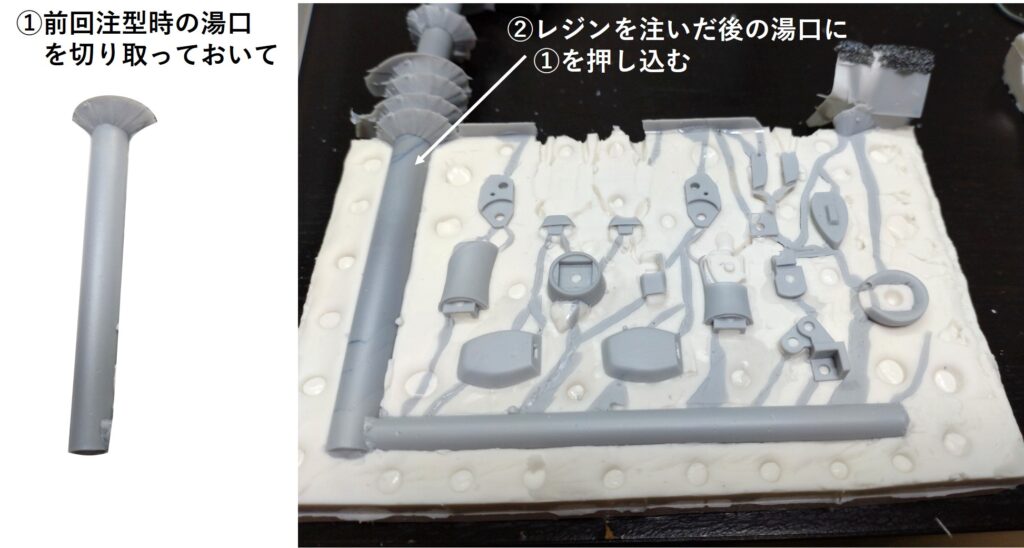
ただこの方法は湯口から大量にレジンがあふれ出てしまうという難点があります。
あふれ出るだけだったらいいのですが、あふれ出たレジンが直近の空気抜け出口をふさいでしまい、結局成形不良が発生してしまうことも多いです。
実際にこの方法で進めるなら湯口周囲にレジンたまりを作れるようなレイアウトにする方がよいと感じています。私自身その改善点に取り組めていないので、次回シリコン型作成時にうまくいったらまたまとめていきたいと思います。
最後に
今回は私自身が型を作った際に実感したトラブル改善方法について書いてみました。
わかった風に書いていますが実際に作って失敗して、そのうえでこういうことだろうと考えた仮説レベルの内容が多いです。
ただこうしてまとめてみると自分の中で重要な点が理解できますし、次回型作成時に事前に振り替えることもできるので非常に良いと思いました。
みなさんも自作の部品ができたら、ぜひ型取り・複製にチャレンジしてみてください。
ではっ!
コメント