こんにちは、MIBです!
以前アイロンを使ったヒートプレスを紹介しました。
電気コンロなど大がかりな機器を使わずに、比較的家庭にあるであろうアイロンを使ってプラ板を軟化させることでお手軽にヒートプレスするというものでした。
スポンジで押し付けて型を取ったり、通常のヒートプレスのように枠に貼り付けたプラ板を押し付けたりして、なかなかものになってきたと感じています。
今回はそんなアイロンヒートプレスを使ってデスフィズ胸部を作成したのでその内容を紹介します。
作成方針
天面が平面で各側面が立ち上がっているので一度のヒートプレスで形にするのは難しいと考え、各面ごとにヒートプレスすることにしました。
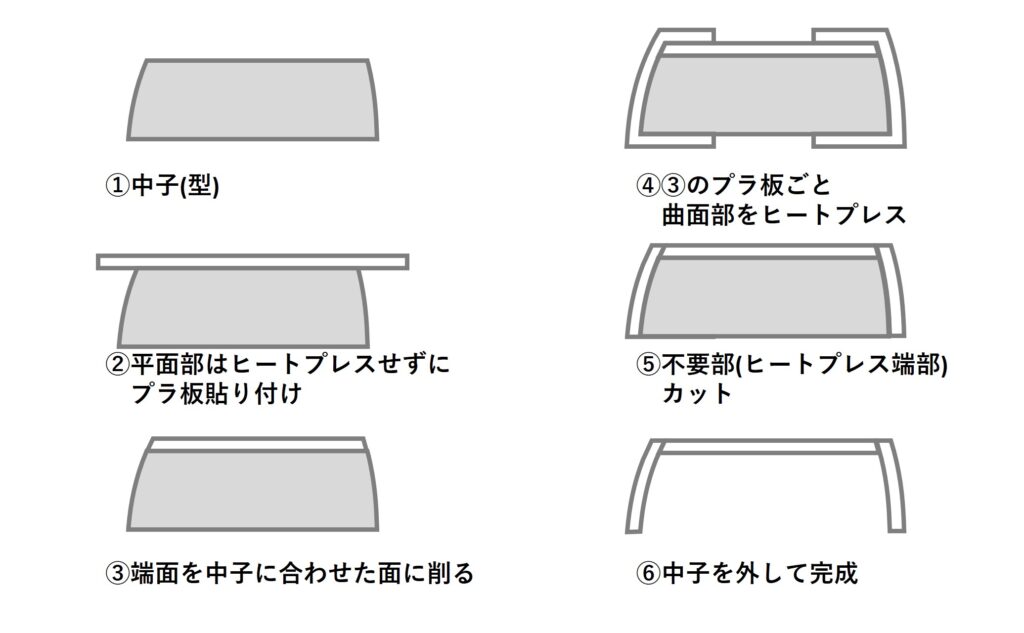
型の製作
ヒートプレスするには何かしらの中子(型)が必要です。前回はプラ板で枠を作ってエポパテで隙間を埋めることで作成しましたが、今回はALLプラ板で作りました。
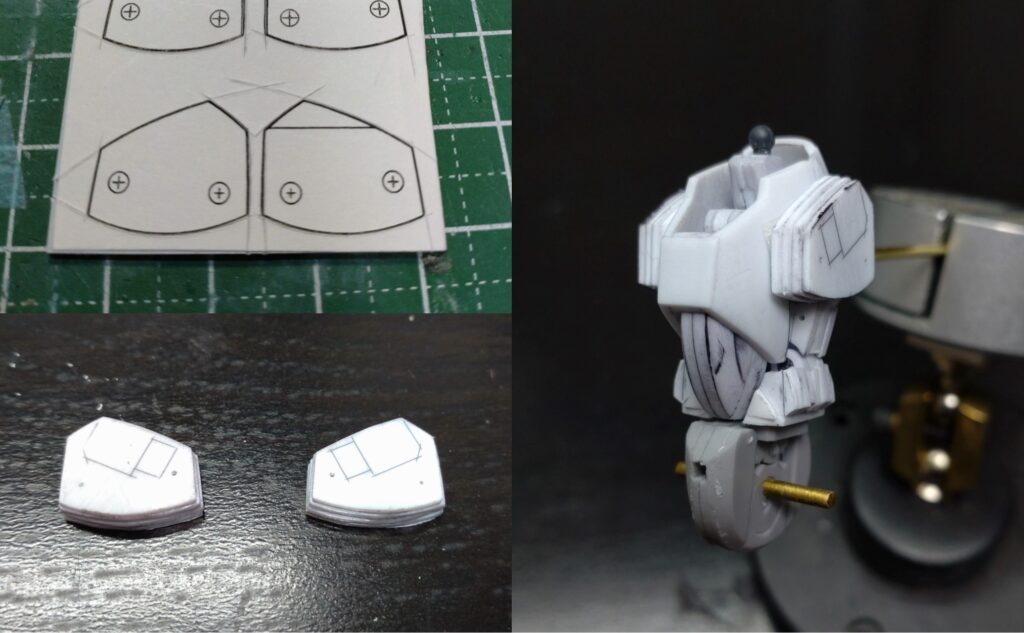
平面部の作成
平面部はヒートプレスする必要がないのでプラ板で作成します。大まかな形状でプラ板を切り出して、型に瞬着の点付けで固定しました。ついでに肩関節を通す穴も開けておきました。
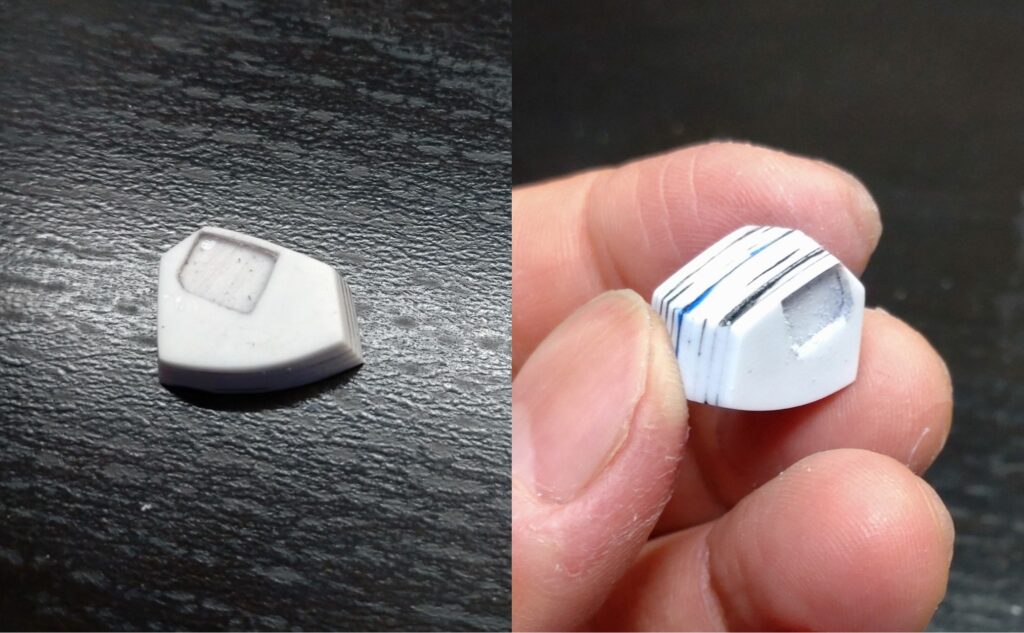
貼り付けた後、端部は各面に添わせるように整形してヒートプレスに備えました。
各面をアイロンヒートプレス
やりやすそうな広い面からアイロンヒートプレスを行っていきます。
主なアイロンヒートプレスのやり方は以下の記事をご確認ください。
やりやすそうな面として、広い面を選びながら進めていきました。

1つの部品で複数面をアイロンヒートプレスで形作る際は隣り合う面は後回しにして、1つ飛ばしで面をヒートプレスしていく方が仕上りがきれいになります。
それは隣の面はヒートプレスしたプラ板の端面を型の面に添わせてからヒートプレスができるので、なるべく多くの面を一度に面加工することが可能だからです。
文字にするとわかりにくいですが下の図を見てください。
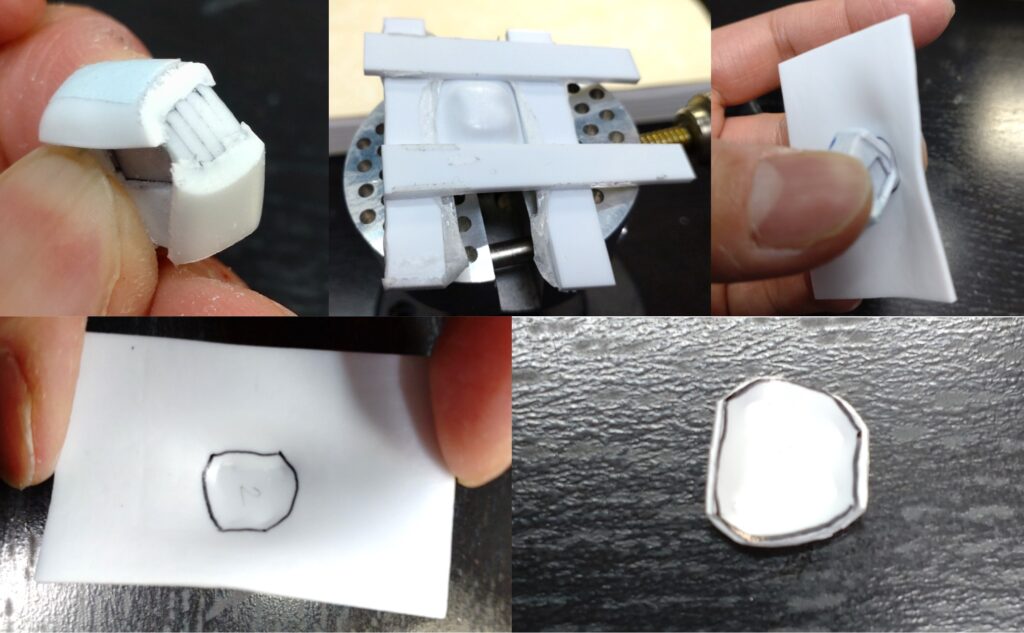
また今回、ヒートプレスの際にバイスで型を固定したことで、とても安定して作業ができました。
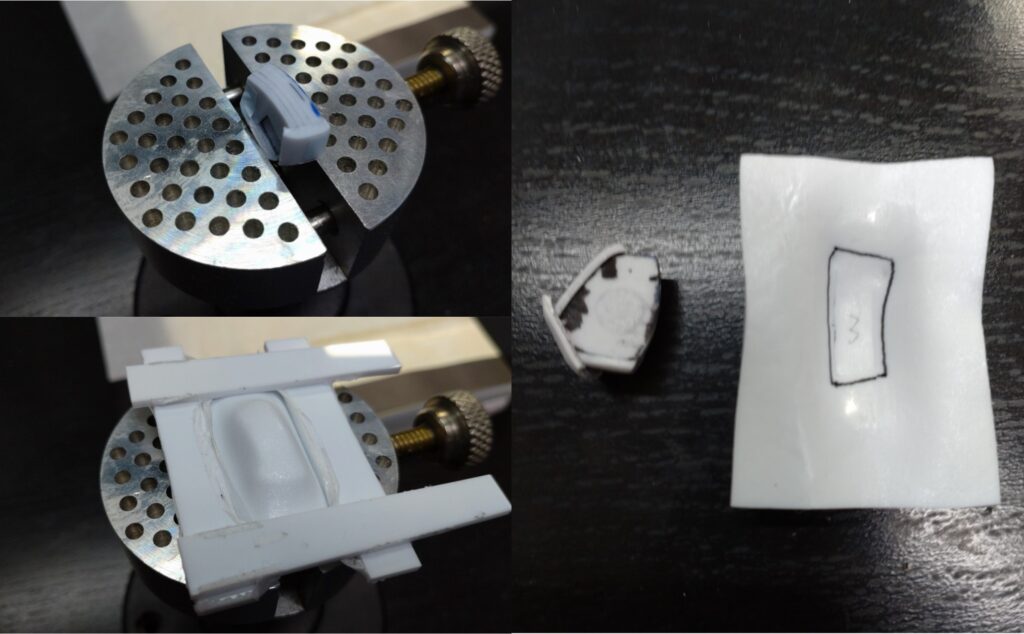
このように各面をヒートプレスして面ごとに接着して、大まかに部品形状が完成しました。
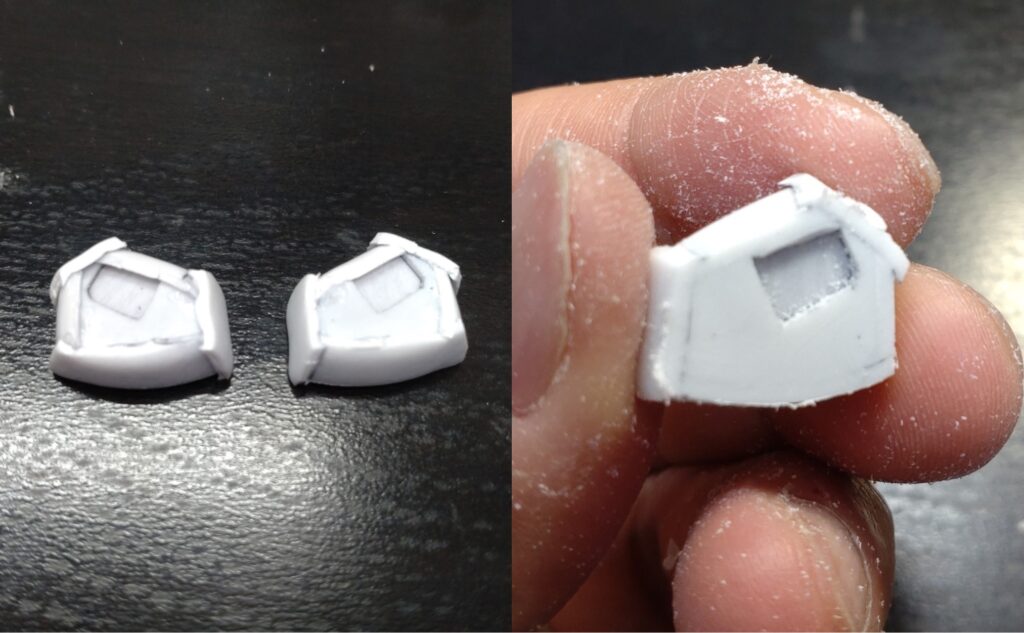
この段階ではのっぺりしてうまく形になるか不安ですが、信じて各面の不要部分を削っていきます。
するとたいてい意外といい形に仕上がります。
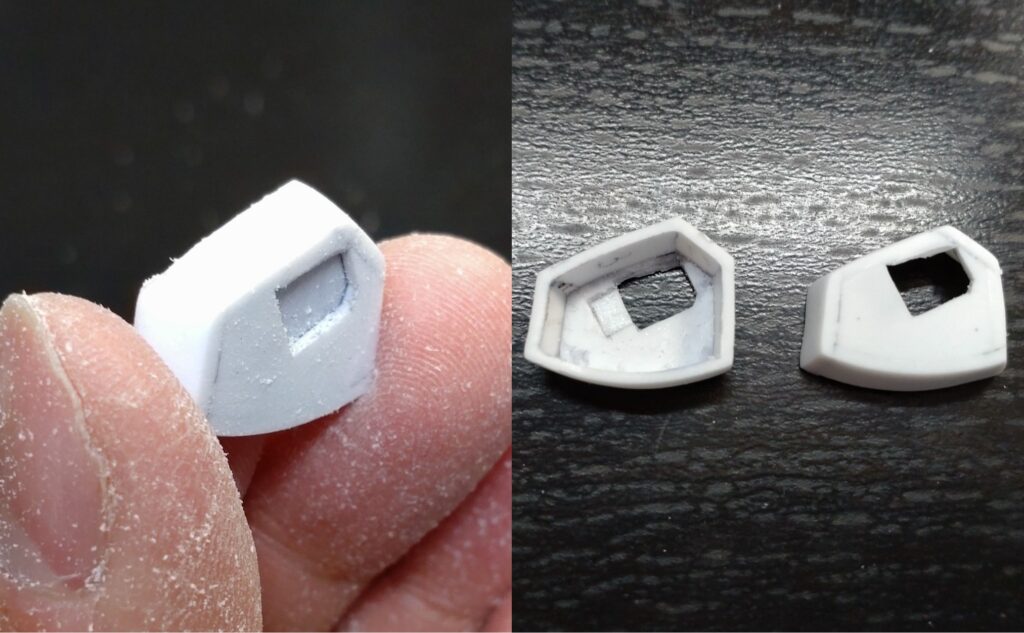
部品としての仕上げ
アイロンヒートプレスを使って部品が形になったので仕上げていきます。
まずは接続ダボを埋め込みます。
プラ棒を貫通させて接着することで狙いの位置に固定できるようにします。
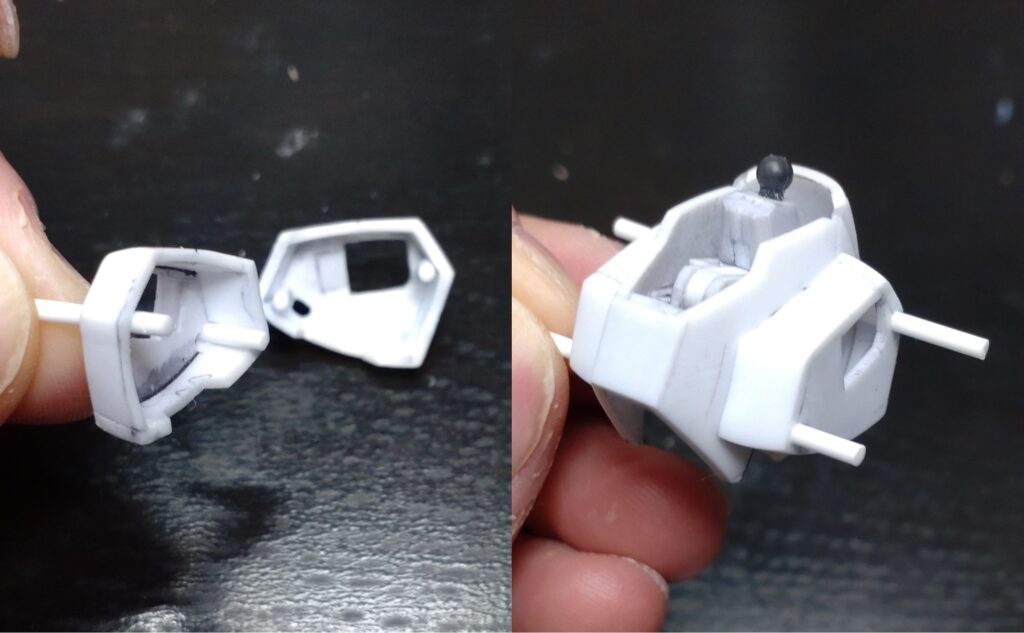
次に細かなディテールを入れていきます。
デスフィズは胸部にギザギザの凹みがあるので、それを削り出していきます。
左右をできるだけそろえるためにマスキングテープで形状を切り出して貼り付けてからカッターで切れ込みを入れて掘っていきました。
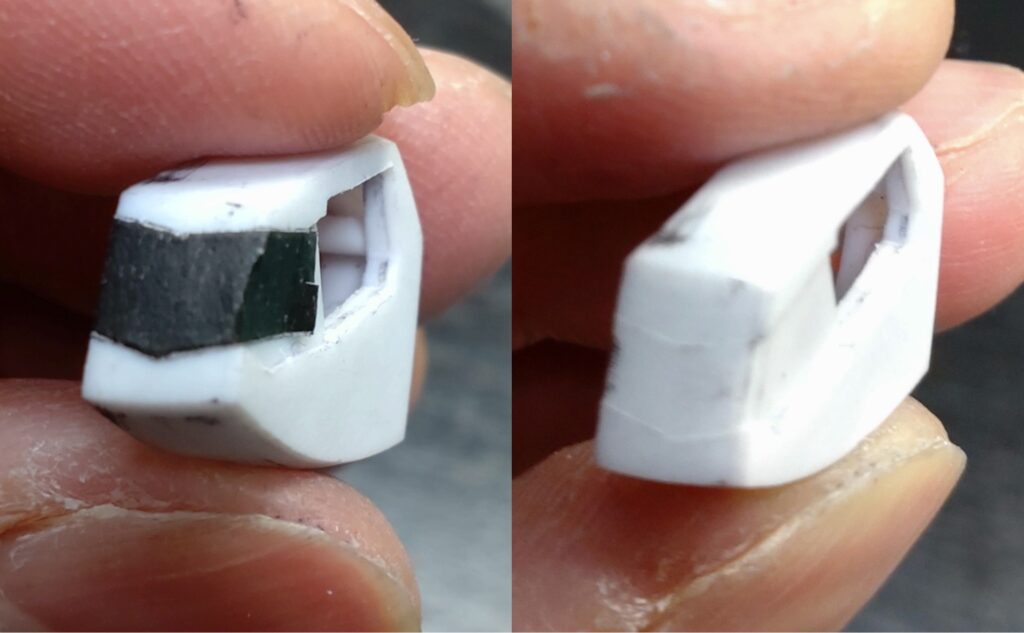
次に各面に丸みを持たせます。
エッジを面取りして、その面のエッジをスポンジやすりで丸みを持たせるように削り出していきます。
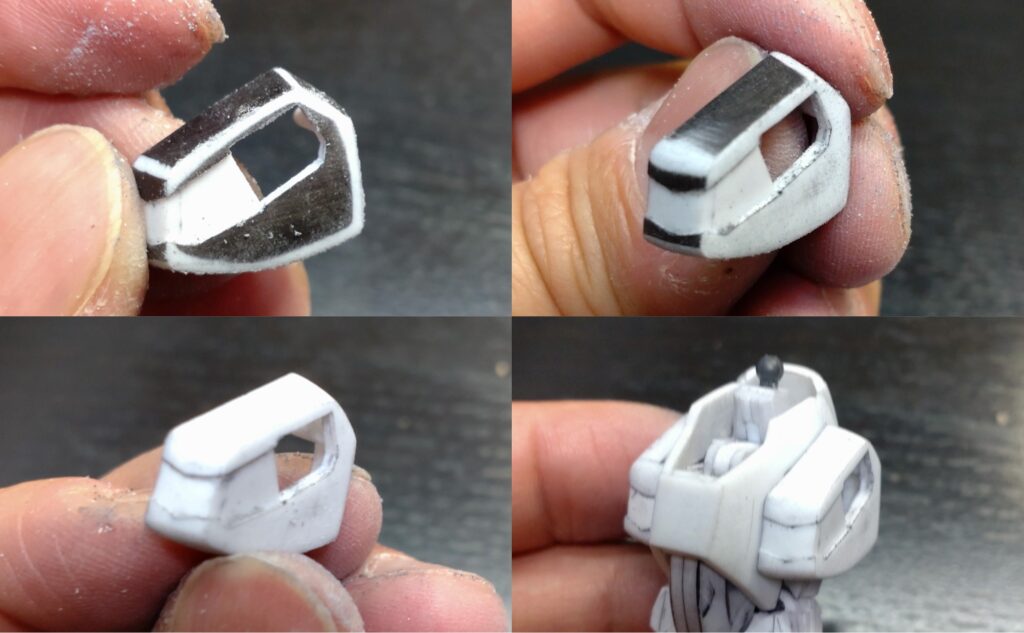
こういう作業の時は漠然と作業すると単にエッジがダルい印象になってしまうので、削りたい形状をイメージして作業することが大事だと考えています。
ここまでの作業で外観はほぼ完成です。
可動部の設置と仮組み
肩関節の可動用に、前方にせり出す位置にポリキャップを設置しました。
一昔前のHGシリーズでよくあった関節です。
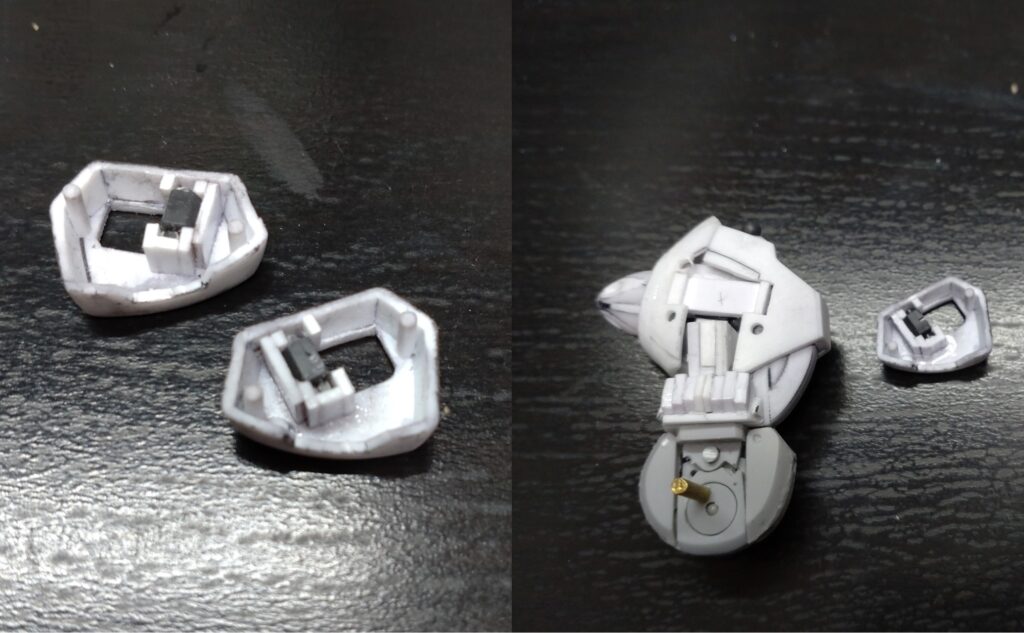
ここまでで胸部が完成しました。
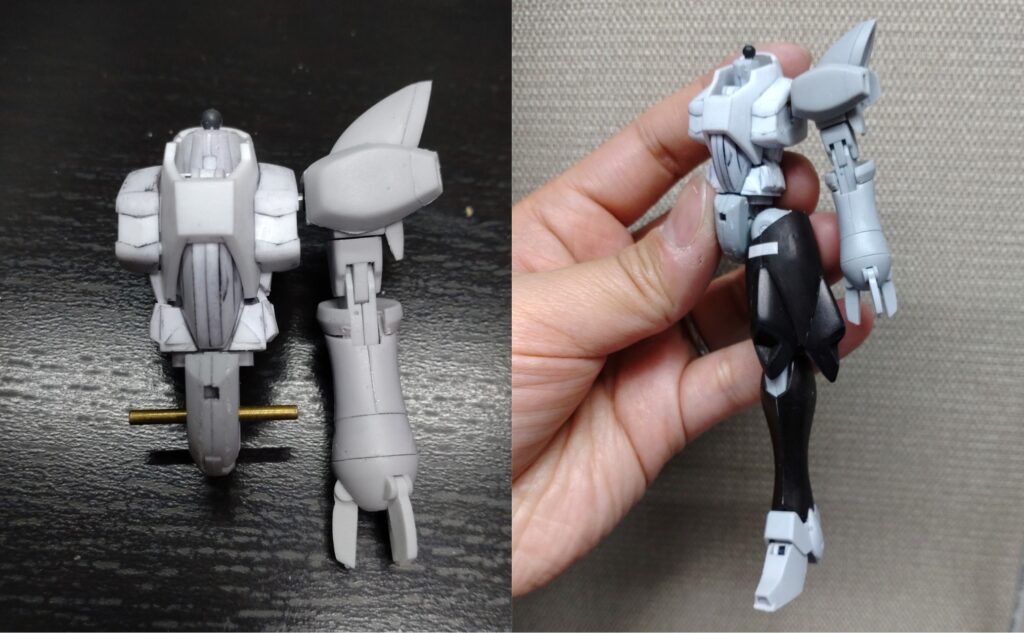
さいごに
アイロンヒートプレス、かなり使いこなせるようになってきた印象です。
私の環境だとやろうと思ったときにすぐにできるので本当に重宝しています。
デスフィズは曲面の多い機体のため完成させるまでにまだまだ使いどころはある気はしているので、
よりやりやすい方法を考えながら取り組んでみたいと思います。
ではっ!
コメント